The world today is gaining a deeper appreciation for EV (Electric Vehicle) technology and its adoption. However, the article gives an overview of the major design and manufacturing challenges that need to be addressed in the sector.
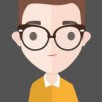
Lorem ipsum dolor sit amet, nec in adipiscing purus luctus, urna pellentesque fringilla vel, non sed arcu integer, mauris ullamcorper ante ut non torquent.
The open adoption of EV technology continues to be the backbone of how the industry operates. But the sub-industry is faced with real-time challenges across regulation, design, and manufacturing.
Here’s a quick overview…
Lithium batteries have been in use for over two decades wherein the energy density of the cells makes them dependable and cost-effective. The main two challenges that influence the sector are when these batteries are at their design stage and when they are at their manufacturing stage.
Design Challenges
- CKD Models:
The EV market in India is based on the CKD model. Sometimes in order to reduce import duty, OEM imports the entire EV in segments and assembles it in India. In order to demonstrate various buying options to the customers, companies may import EVs with different design options on the same voltage platform. The ignored part is that even though the voltage is the same, every other EV will need a different battery design since the chassis design is different.
- The absence of standard protocols:
The Lithium battery segment is divided into two sections – high and low voltage. There are standard protocols in place for high voltage batteries, since high-speed EV manufacturers that use them need proper certification from the government. However, the low voltage batteries that are used by low-speed EVs do not have certifications in place, leading to the neglect of standard protocols across the use of the type of connectors, wires, battery testing, and standards.
- Sheet metal challenges within the purview of battery design:
The thickness and strength of the sheet metal are important. When the thickness is increased, the overall load of the EV battery increases, which further increases the rate of battery discharge. When the thickness is decreased, it’s quite possible that the battery box will get destroyed, since the weight of the cells will impact the battery box.
- The need for highly-skilled technical talent:
As the newness of the Lithium Battery manufacturing industry is on its onset and developing, there are not many professionals required to design these batteries.
Challenges Across Manufacturing and Supply Chain
- Supply chain challenges:
India lacks a lithium cell manufacturing capacity, so companies that manufacture battery packs are importing the cells from China or other parts of the world. Battery Management System (BMS) is a technology dedicated to the oversight of a battery pack. Due to the global shortage of semiconductors, a demand and supply gap has been created that affects the production of BMS.
- Logistical challenges:
These can be better understood when we understand how COVID-19 pandemic has had its effects on the global supply networks. Also, the impact of logistical and supply chain operations on the environment is being recognized as a matter of concern. In order to reach their emissions objectives, governments must have stable supply chain practices. Due to these logistics issues, freight charges have escalated, which in turn affects the price of components used to make the Lithium-ion batteries.
Role of the Government of India
There has undoubtedly been a positive shift in policy and the adoption of EVs in the country. India is working towards setting up an industry that manufactures EVs locally.
An upfront reduction in the purchase price of the EVs under the FAME- India scheme is an incentive provided to buyers of EVs.
The incentive subsidies linked to the battery capacity for E-TwoWheeler were increased to Rs 15,000/ KWh (US$ 199.56/KWh) which was previously Rs 10,000/KWh (US$ 133.04/KWh).
The various initiatives taken by the government to promote Electric Vehicles in India are as follows…
1) GST on the electric vehicles and the chargers/ charging stations has been reduced from 12% to 5% and from 18% to 5%, respectively.
2) A notification has been released by the Ministry of Power regarding charging infrastructure standards permitting private charging at residences and offices.
3) Battery-operated vehicles will be given green licence plates and be exempted from permit requirements, as announced by the Ministry of Road Transport & Highways (MoRTH).
4) A notification advising states to waive road tax on EVs has been issued by MoRTH, leading to a reduction in the initial costs of EVs.
5) Model Building Bylaws 2016 was amended to establish charging stations and infrastructure in private and commercial buildings by the Ministry of Housing & Urban Affairs (MoHUA).
Your Comment Please